The Power of Liquid Silicone Injection Molding Machines in Today's Industries
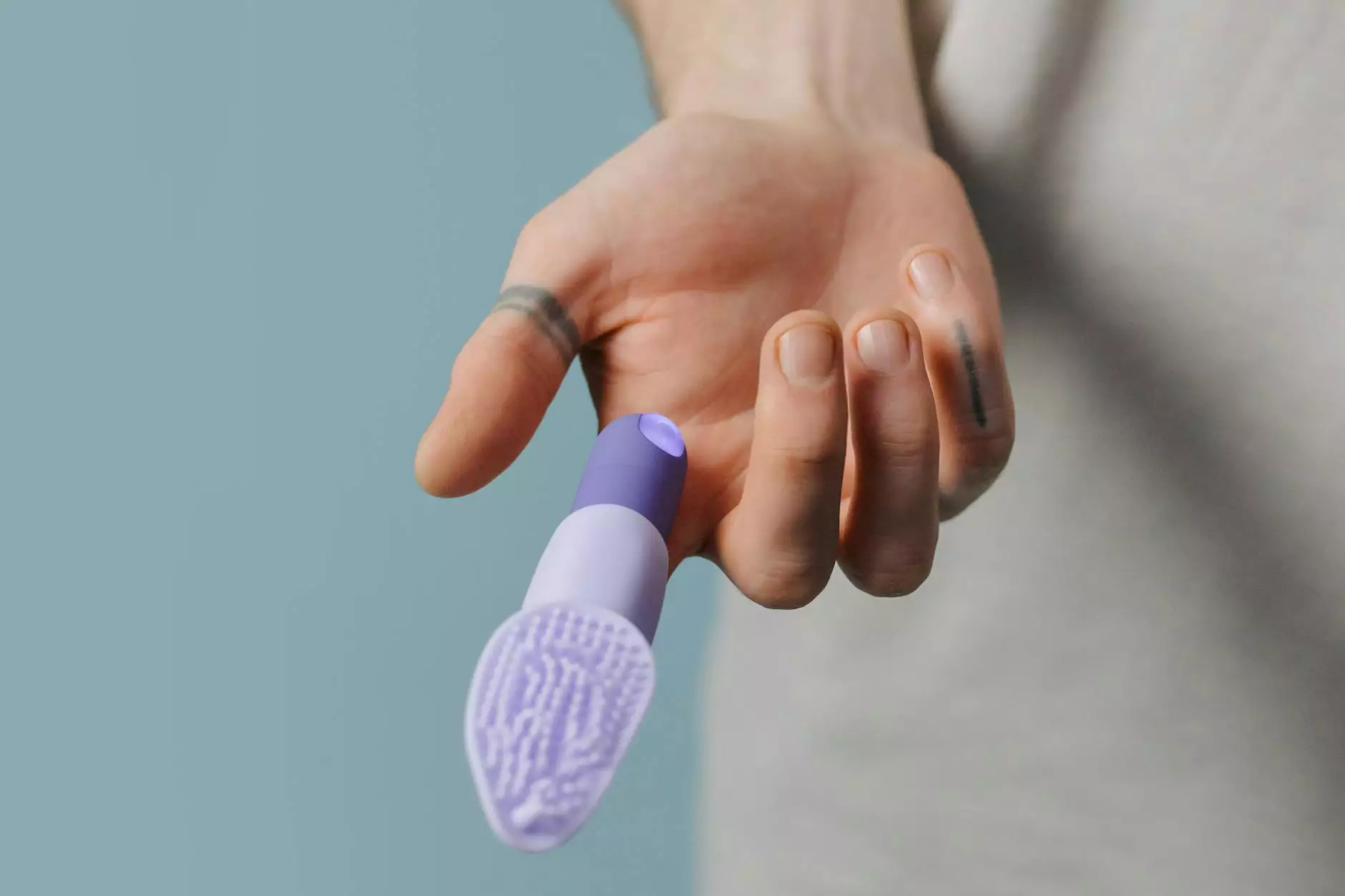
In the constantly evolving landscape of manufacturing, the demand for precision, efficiency, and versatility is higher than ever. Amidst this backdrop, the liquid silicone injection molding machine has emerged as a pivotal technology, especially for industries like electronics and medical supplies. This article explores the functionalities, advantages, and applications of these machines, paving the way for a brighter future in manufacturing.
Understanding Liquid Silicone Injection Molding
Liquid silicone injection molding (LSR molding) is a process that utilizes liquid silicone rubber to create precision parts in a variety of applications. Unlike traditional injection molding with thermoplastic materials, LSR molding offers unique benefits that make it suitable for demanding applications, especially where durability and flexibility are required.
What is Liquid Silicone Rubber (LSR)?
Liquid silicone rubber is a high-performance material that exhibits remarkable properties:
- Temperature Resistance: LSR can withstand extreme temperatures, making it ideal for a variety of applications.
- Chemical Resistance: Its resistance to many chemicals and solvents ensures longevity and durability.
- Biocompatibility: LSR is commonly used in medical applications due to its compatibility with human tissue.
- Flexibility and Elasticity: The material is highly flexible, making it great for parts that require bending and stretching.
The Liquid Silicone Injection Molding Process
The typical process of liquid silicone injection molding includes:
- Preparation: The LSR is mixed with a curing agent.
- Injection: The liquid silicone is injected into a mold where it cures into a solid state.
- Curing: The combination of heat and pressure helps to solidify the silicone.
- Cooling and Removal: Once cured, the part is cooled and then carefully removed from the mold.
Benefits of Using Liquid Silicone Injection Molding Machines
Investing in a liquid silicone injection molding machine brings numerous benefits:
1. Precision and Quality
LSR molding can produce intricate and detailed components with high precision, minimizing the possibility of defects. This quality control is critical for industries such as electronics and medical supplies, where accuracy is paramount.
2. High Production Efficiency
With automated processes and quick curing times, liquid silicone injection molding machines are capable of producing a large volume of parts in a short period, increasing operational efficiency.
3. Cost-Effectiveness
The durability and lifespan of LSR products often lead to lower overall costs. Although initial investments may be higher, savings on materials and replacements make it a cost-effective choice in the long run.
4. Sustainability
Liquid silicone rubber is a sustainable material that can be reused and recycled, reducing waste and environmental impact significantly.
Applications in the Electronics Industry
The electronics industry has seen remarkable innovations due to the adaptability of liquid silicone injection molding machines. Some key applications include:
1. Seals and Gaskets
LSR is an ideal material for producing seals and gaskets that require water and air-tight features. Its flexibility ensures snug fits in various electronic devices, enhancing their longevity.
2. Keypads and Buttons
Liquid silicone molding allows for the creation of tactile, soft-touch buttons and keypads. The material can be colored and textured, enhancing user experience while maintaining functionality.
3. Insulation and Protection
Silicone provides excellent electrical insulation properties, making it suitable for protective housings and covers for sensitive electronics, protecting them from moisture and dust.
Applications in the Medical Supplies Industry
The medical sector is another realm where liquid silicone injection molding machines excel, primarily due to the biocompatibility of LSR. Notable applications include:
1. Medical Devices
LSR is extensively used to manufacture components for medical devices, including tubing, catheter parts, and valves, which require both precision and hygiene.
2. Personal Protective Equipment (PPE)
With the increasing importance of PPE, liquid silicone's flexibility and durability have found applications in producing masks, gloves, and other protective gear essential in medical environments.
3. Surgical Tools
Liquid silicone is also utilized in the production of various surgical tools and instruments, proving its efficacy and reliability in life-saving situations.
Future Trends in Liquid Silicone Injection Molding
The future for liquid silicone injection molding machines looks promising, with several trends shaping the market:
1. Technological Advancements
As technology continues to evolve, newer machines with enhanced capabilities, such as smart automation and higher precision control, will redefine the molding process.
2. Expanding Applications
New applications across various fields, including automotive and consumer goods, are emerging, indicating a broader adoption of LSR. The versatility of the material opens doors to innovative uses.
3. Increased Focus on Sustainability
With environmental concerns on the rise, manufacturers are likely to focus more on sustainable practices, including the use of eco-friendly silicone materials and recycling processes in their production lines.
The Role of Nolato in Championing Innovation
As a leader in the realm of injection molding, Nolato stands at the forefront of innovation. With expertise in electronics and medical supplies, Nolato leverages its advanced liquid silicone injection molding machines to deliver top-notch quality parts tailored to the exacting needs of clients.
By investing in state-of-the-art technology and adhering to rigorous industry standards, Nolato ensures that their manufacturing processes not only meet but exceed customer expectations, setting benchmarks in quality and efficiency.
Conclusion
In conclusion, the emergence of liquid silicone injection molding machines has transformed the manufacturing landscape across various industries, particularly in electronics and medical supplies. The benefits of using LSR technology—from its unmatched durability to its vast application spectrum—position it as a vital solution for today’s manufacturing challenges. As advancements continue, industries can look forward to even greater innovations, driven by the capabilities of liquid silicone injection molding machines.
For businesses seeking cutting-edge solutions that deliver efficiency and precision, the integration of LSR molding into production lines promises a competitive edge in a rapidly evolving market. With players like Nolato leading the charge, the future of liquid silicone will be brighter than ever.