The Power of Insert Molding Solutions: Transforming Your Business
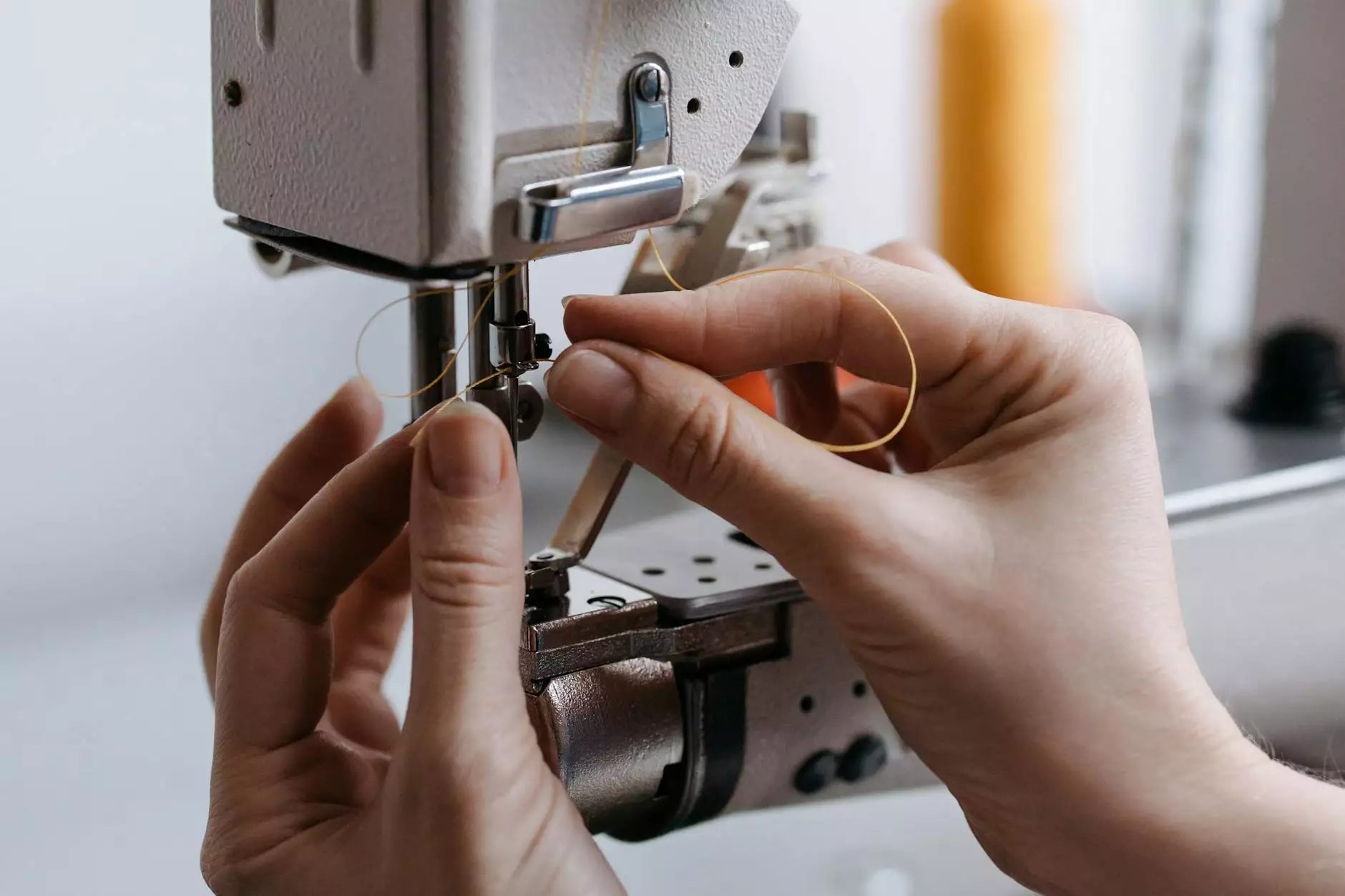
In today's rapidly evolving manufacturing landscape, the demand for insert molding solutions has skyrocketed. Businesses are continually seeking innovative methods to enhance productivity, reduce costs, and improve product quality. Insert molding is a manufacturing process that combines the best of plastic injection molding with the advantages of embedded components. This article will delve into the intricacies of insert molding, explore its benefits, and provide comprehensive insights into how it can revolutionize your operations.
Understanding Insert Molding
Insert molding is an advanced manufacturing technique that involves placing pre-made components, such as metal or plastic parts, into a mold cavity before the injection of molten plastic. This process results in a single, cohesive part that integrates the functions of multiple components. The beauty of this method lies in its ability to enhance product reliability while reducing assembly time.
How Insert Molding Works
- Component Preparation: The first step involves selecting and preparing the components that will be inserted into the mold. This could include metallic inserts like screws or terminals that require encapsulation.
- Mold Design: An expertly designed mold is crucial for successful insert molding. The mold must accommodate both the inserts and the injection of plastic.
- Injection Process: The molten plastic is injected into the mold, encapsulating the previously placed inserts and forming a finished product once cooled.
- Post-processing: After cooling, the part is ejected from the mold, often requiring secondary operations like trimming or surface finishing.
Benefits of Insert Molding Solutions
Choosing insert molding solutions can yield substantial benefits for your business. Below are some compelling reasons to consider this innovative manufacturing process:
1. Cost Efficiency
One of the primary advantages of insert molding solutions is the significant reduction in manufacturing costs. By combining multiple components into a single piece, businesses can minimize labor and assembly costs, ultimately leading to a more efficient production process.
2. Enhanced Product Durability
Insert molding creates strong bonds between the plastic and the embedded components, leading to products that are less prone to failure. This enhances the overall durability and reliability of the end product, reducing the likelihood of returns and warranty claims.
3. Improved Design Flexibility
Insert molding allows for greater design flexibility. Manufacturers can design complex geometries and integrate various materials into a single part. This capability opens new avenues for innovative product designs and functionalities that meet evolving market demands.
4. Streamlined Production Process
By reducing the number of steps in the manufacturing process, insert molding streamlines production workflows. This not only accelerates time-to-market but also strengthens supply chain efficiency.
5. Weight Reduction
By using less material and combining parts, insert molding can lead to a lighter final product without compromising strength. This is particularly beneficial in industries such as automotive and aerospace, where weight savings can significantly impact fuel efficiency and performance.
Applications of Insert Molding
The versatility of insert molding solutions means they can be applied across various industries. Here are some key applications:
1. Automotive Industry
In the automotive sector, insert molding is widely utilized for manufacturing components such as dashboard assemblies, connectors, and housings. The ability to embed metal parts like terminals and pins enhances structural integrity and manufacturing efficiency.
2. Electronics
Electronics manufacturers benefit from insert molding for producing integrated components like circuit boards, connectors, and housings for various devices. This process shields sensitive electronic components from environmental factors while ensuring a robust assembly.
3. Medical Devices
The medical device industry utilizes insert molding for producing components that require precision and reliability, such as syringe bodies and catheter housings. The ability to integrate various materials into a single part is essential for meeting regulatory standards and safety requirements.
4. Consumer Products
Consumer products such as household appliances and tools often involve insert molding for creating ergonomic grips and integrated assembly components. This leads to improved user experience and product longevity.
The Industry's Best Practices for Insert Molding
To fully harness the potential of insert molding solutions, adopting industry best practices is essential:
1. Collaborate with a Skilled Plastic Mold Maker
Choosing the right plastic mold maker is crucial. A company like Hanking Mould specializes in producing high-quality molds that are key to successful insert molding. Collaboration ensures that all components fit perfectly and that the mold functions efficiently.
2. Invest in Quality Materials
Using high-quality materials enhances the performance of insert molded parts. Ensure that plastics and inserts meet industry standards and are suitable for the intended application.
3. Focus on Precision Engineering
Precision is vital in insert molding. Monitoring and controlling variables such as temperature, pressure, and cycle times can significantly affect the quality of the final product. Investing in state-of-the-art machinery can aid in achieving optimal results.
4. Implement Quality Control Measures
Regular quality checks throughout the production process can help identify imperfections early, ensuring that only top-quality products reach the market. Implementing rigorous testing protocols is essential for maintaining high standards.
Conclusion: Elevating Your Business with Insert Molding Solutions
Insert molding solutions present a unique opportunity for businesses to enhance their manufacturing processes. From cost efficiency and product durability to design flexibility and streamlined production, the benefits are substantial. By adopting insert molding, companies can not only improve product quality but also gain a competitive edge in the market.
For businesses looking to adopt this innovative technology, partnering with a reputable plastic injection mould manufacturer is essential. Hanking Mould stands ready to provide expert solutions tailored to your needs, ensuring that you remain at the forefront of your industry. Embrace the future of manufacturing with insert molding solutions and take your business to new heights.